Metal tubing fluid lines are sized by wall thickness and – Metal tubing fluid lines, ubiquitous in various industries, are meticulously engineered to ensure the efficient and safe conveyance of fluids. The wall thickness of these lines plays a pivotal role in determining their performance, influencing fluid flow, pressure handling capabilities, and overall reliability.
This comprehensive guide delves into the intricacies of metal tubing fluid line sizing, exploring the factors that govern wall thickness determination, the influence of material selection, and the significance of design considerations. By understanding these concepts, engineers and technicians can optimize fluid line systems for specific applications, ensuring longevity, efficiency, and adherence to industry standards.
Wall Thickness and Fluid Line Sizing
The wall thickness of metal tubing fluid lines is a crucial factor in determining their performance and reliability. It directly influences the flow rate, pressure capacity, and overall structural integrity of the system.
Thicker walls provide higher resistance to internal pressure and external forces, allowing for higher fluid flow rates and pressures. However, they also increase the weight and cost of the tubing. Thinner walls, on the other hand, are lighter and more economical but may be more susceptible to deformation and leaks under high pressure or stress.
Determining Wall Thickness
The determination of wall thickness for metal tubing fluid lines involves considering several factors:
- Pressure:The maximum pressure that the fluid line will experience during operation. Higher pressures require thicker walls to prevent bursting or leakage.
- Temperature:Extreme temperatures can affect the material properties of the tubing and weaken the walls. Thicker walls are necessary for applications with high or low temperatures.
- Fluid properties:The viscosity, density, and corrosiveness of the fluid being transported can impact the required wall thickness. More viscous fluids require larger diameters, while corrosive fluids may necessitate thicker walls to resist chemical attack.
Standards and Regulations, Metal tubing fluid lines are sized by wall thickness and
To ensure safety and reliability, metal tubing fluid lines must comply with relevant standards and regulations. These standards provide guidelines for material selection, wall thickness calculations, and testing procedures.
Some common standards include:
- ASME B31.1: Power Piping
- ASME B31.3: Process Piping
- ANSI/ASME B36.10M: Welded and Seamless Wrought Steel Pipe
Material Selection
The type of metal used in the manufacturing of metal tubing fluid lines depends on the specific application requirements.
- Stainless steel:Corrosion-resistant, high-strength, and suitable for a wide range of fluids and environments.
- Carbon steel:Economical, durable, and commonly used for low-pressure applications.
- Copper:High thermal conductivity, corrosion resistance, and antimicrobial properties.
- Aluminum:Lightweight, corrosion-resistant, and suitable for low-pressure applications.
Design Considerations
The design of metal tubing fluid lines involves several key considerations:
- Bending radius:The minimum radius to which the tubing can be bent without kinking or weakening the walls.
- Connection types:The type of connections used to join tubing sections, such as threaded, flanged, or welded.
- Support:Proper support is essential to prevent excessive vibration or sagging, which can lead to leaks or damage.
Installation and Maintenance
Proper installation and maintenance are crucial for the longevity and performance of metal tubing fluid lines.
- Handling:Avoid rough handling or excessive bending that could damage the tubing.
- Routing:Plan the routing carefully to minimize stress on the tubing and avoid potential hazards.
- Support:Provide adequate support throughout the entire length of the tubing to prevent sagging or vibration.
Troubleshooting
Common problems that can occur with metal tubing fluid lines include:
- Leaks:Can be caused by loose connections, damaged tubing, or corrosion.
- Blockages:Can be caused by debris, scale, or foreign objects in the fluid.
- Corrosion:Can be caused by exposure to corrosive fluids or environments.
Case Studies
Numerous successful applications of metal tubing fluid lines can be found across various industries.
Case Study 1:The use of stainless steel tubing in a high-pressure hydraulic system in a manufacturing plant. The thicker walls of the tubing ensured reliable operation under extreme pressures.
Case Study 2:The use of copper tubing in a chemical processing plant. The corrosion resistance of copper made it suitable for handling corrosive fluids.
General Inquiries: Metal Tubing Fluid Lines Are Sized By Wall Thickness And
What is the relationship between wall thickness and fluid flow in metal tubing fluid lines?
Wall thickness directly impacts fluid flow rate. Thicker walls restrict flow due to increased friction, while thinner walls promote smoother flow with reduced pressure drop.
How does pressure influence wall thickness determination?
Higher operating pressures necessitate thicker walls to withstand the increased internal forces, ensuring structural integrity and preventing catastrophic failures.
What role does temperature play in wall thickness calculations?
Temperature affects the material properties of the tubing. At elevated temperatures, materials may weaken, necessitating thicker walls to maintain structural stability.
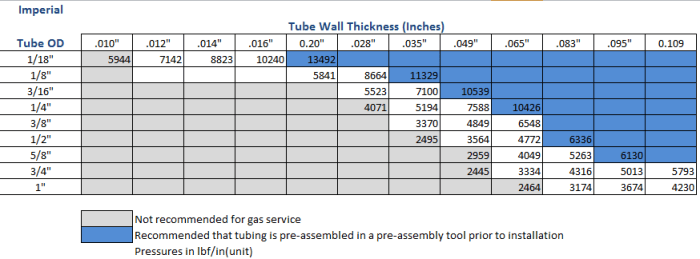
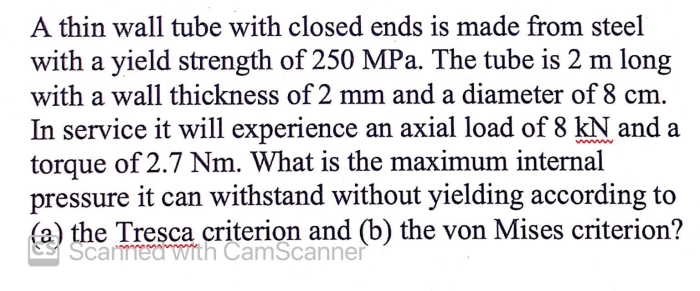
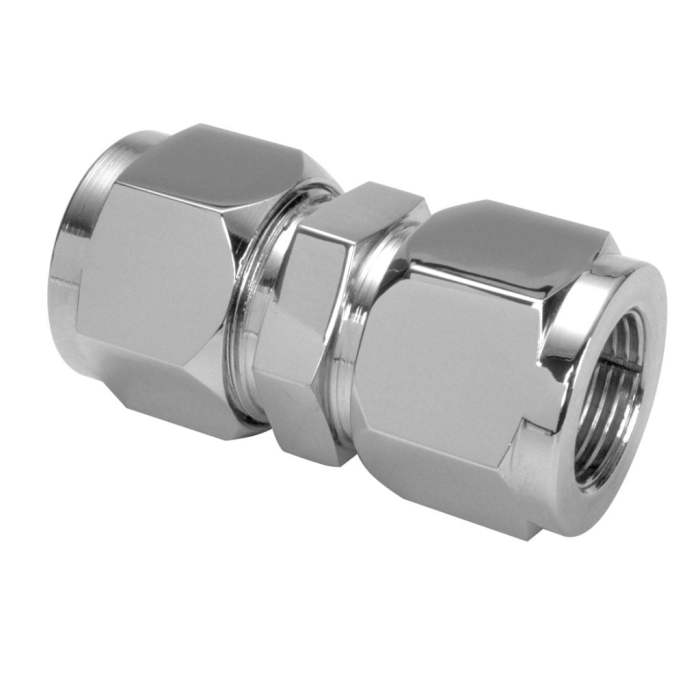